In the world of advanced manufacturing, precision and efficiency are paramount. The OMAX 120X Precision JetMachining Center stands out as a cutting-edge solution for large-scale or multiple-part projects. This review delves into its features, performance, and user experience to provide a thorough analysis of its capabilities and benefits.
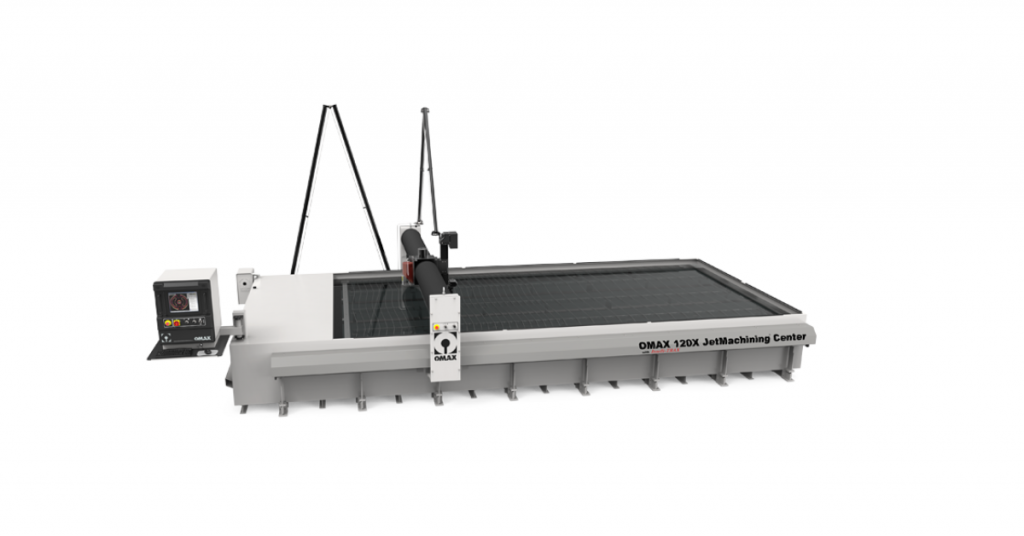
OMAX 120X Abrasive Water Jet Specifications
Specification | Details |
---|---|
Footprint (with Pump) | 33′ 3″ x 19′ 5″ to 51′ 6″ x 22′ 5″ (10.13 m x 5.92 m to 15.70 m x 6.81 m) |
Height (with Scissor Plumbing) | 14’0″ (4.27 m) |
Operating Weight | 71,679 lbs to 123,453 lbs (32,513 kg to 55,997 kg) |
Weight (Tank Empty) | 22,000 lbs to 34,000 lbs (9,979 kg to 15,422 kg) |
X-Y Cutting Travel | 20′ x 10′ to 40′ x 10′ (6.09 m x 3.04 m to 12.19 m x 3.04 m) |
Z-Axis Travel (with Motorized Z Axis) | 8″ (203 mm) |
Table Size | 21′ x 11’5″ to 41′ x 11’5″ (6.40 m x 3.48 m to 12.50 m x 3.48 m) |
Material Supports Slats | 4″ x 1/8″ Galvanized Steel |
Maximum Supported Material Load | 400 lbs/sq ft (1,950 kg/sq meter) |
Electrical Requirements | 3-Phase, 380-480 VAC ±10%, 50-60 Hz |
Noise Level | Below 80 dBA at one meter for submerged cutting |
Speed | 350 in/min (8,890 mm/min) |
Linear Positional Accuracy | ±0.001″ (±0.025 mm) |
Repeatability | ±0.001″ (±0.025 mm) |
Ballbar Circularity | ±0.005″ (±0.127 mm) |
Quick Features Look
Standard Features
- IntelliMAX Premium Software: Backed by our exclusive software, enhancing operational efficiency and ease of use.
- IntelliTRAX System: Features an exclusive abrasive jet linear drive system that delivers speeds up to 350 in/min (8.9 m/min) with real-time closed-loop positioning feedback for precision.
- Programmable Z-Axis: Offers a 12-inch (305 mm) programmable Z axis, boasting the lowest ceiling height requirement in the industry.
- Rapid Water Level Control: Standard feature that ensures cleaner, safer, and quieter submerged cutting, typically maintaining noise levels below 80 dBA.
OMAX Benefits
- Local Manufacturing: Designed and manufactured at the OMAX factory in Kent, Washington, USA, ensuring high quality and reliability.
- No Heat-Affected Zones: The cutting process does not create heat-affected zones or mechanical stresses, preserving the integrity of the materials.
- Versatile Material Handling: Capable of machining a wide range of materials and thicknesses, including metals, composites, glass, and plastics.
- Efficient Setup: Requires no tool changes and minimal fixturing, which significantly reduces setup time.
Service & Training
- Lifetime Training: Unlimited free training for the life of your machine, ensuring your team is always up to speed with the latest operational techniques.
- Software Upgrades: Unlimited software upgrades are provided for the life of the machine, keeping it current with the latest improvements.
- Warranty: Comes with a 2-year / 4000-hour limited warranty, offering peace of mind and protection for your investment.
- Onsite Training: Includes 3 days of onsite training upon installation to ensure your team is fully equipped to use the machine effectively from day one.
Overview
The OMAX 120X is a robust abrasive water jet cutter designed for full-scale production. It can handle everything from metals and composites to glass and plastics without creating heat-affected zones or mechanical stresses. With its range of lengths from 33′ 3″ to 51′ 6″, this machine is versatile and capable of accommodating large-scale industrial applications.
Cutting Technology and Precision
At the heart of the OMAX 120X’s efficiency is its advanced IntelliTRAX linear drive technology, which is tailored specifically for the harsh environments of abrasive waterjet cutting. This system ensures exceptional precision with a linear positional accuracy of ±0.001″ (±0.025 mm). Supported by real-world cutting data, the 120X boasts the fastest cutting speeds and best precision in the industry. The programmable Motorized Z-Axis, equipped with the precision OMAX MAXJET 5i Nozzle, further enhances productivity and process efficiency.
Features and Design
Standard Features:
- The IntelliMAX Premium Software backs the system, streamlining operations and maximizing output.
- Rapid Water Level Control allows for cleaner, quieter, and safer submerged cutting, typically maintaining a noise level below 80 dBA.
- The inclusion of a 600 lb Bulk Abrasive Delivery System ensures continuous operation by efficiently transporting garnet from a large hopper to the Zero Downtime Hopper on the Z-Axis.
- Scissor-style hard plumbing and the sealed drive system protect against water, dirt, and grit, which are common in industrial environments.
Optional Features:
- DualBRIDGE System: This optional feature doubles the machining capacity, making the 120X even more versatile for handling expansive projects.
Performance and Usability
The 120X is not only powerful but also designed with user experience in mind. The control software is intuitive, allowing for easy operation and minimal training. OMAX offers unlimited free training for the life of the machine and unlimited software upgrades, ensuring that users can continually leverage the latest advancements in technology. Moreover, the installation includes three days of onsite training, which is a significant value-add for any operation.
Maintenance and Sustainability
OMAX emphasizes low maintenance and high reliability with the 120X. The high-efficiency Generation 4 EnduroMAX pump, which can be upgraded to 100 hp, operates with up to 85% efficiency and requires maintenance only every 1,000 hours. The machine’s design and materials, including 4″ x 1/8″ galvanized steel material supports slats, ensure durability and a reduced need for frequent upkeep.
From an environmental perspective, the OMAX 120X is designed to operate cleanly and quietly, with no noxious gases, liquids, or oils used in the machining process. This makes it an ideal choice for operations looking to reduce their environmental footprint while maintaining high standards of cleanliness and noise control.
Installation and Support
The OMAX 120X is hefty, with operating weights ranging from 71,679 lbs to 123,453 lbs, and requires a substantial installation space. However, its design minimizes the footprint relative to its capabilities, making it a viable option for facilities with limited space but high-capacity needs.
OMAX’s commitment to customer support is evident in its warranty and service offerings, including a 2-year / 4000-hour limited warranty. The availability of extensive training and support helps users maximize the machine’s capabilities and ensures a quick resolution of any issues.
Advanced Software Integration
A pivotal aspect of the OMAX 120X is its integration with IntelliMAX Premium Software. This software suite is a cornerstone of OMAX technology, designed to optimize the machine’s performance and ease of use. It provides a user-friendly interface that allows operators to quickly convert complex CAD designs into precise cutting instructions. This seamless translation from design to execution minimizes setup time and enhances the overall workflow efficiency.
Innovative Design Elements
The design of the OMAX 120X reflects a deep understanding of the needs of high-volume manufacturing environments. The standard programmable Motorized Z-Axis is a testament to this, allowing for automated adjustment of the cutting head, which is essential for managing varied material types and thicknesses without manual intervention. Additionally, the Rapid Water Level Control feature not only maintains a quiet workspace but also minimizes splash and allows for faster switching between different cutting jobs.
DualBRIDGE System: A Closer Look
For facilities that handle exceptionally large or complex projects, the optional DualBRIDGE System offers a significant enhancement. This feature effectively doubles the machine’s processing area and allows for simultaneous cutting operations. By integrating a second bridge into the system, users can achieve a substantial increase in output without compromising on the precision for which OMAX is known. This option exemplifies the machine’s scalability and adaptability to growing business needs.
Material Versatility
The ability of the OMAX 120X to cut a wide range of materials cannot be overstated. From titanium and advanced composites to glass and rubber, the machine handles an impressive spectrum of materials. This versatility is crucial for industries such as aerospace, automotive, and manufacturing, where different materials are often processed in the same facility. The OMAX 120X’s capability to switch between materials with minimal setup changes significantly reduces downtime and increases throughput.
Environmental Impact and Operational Efficiency
OMAX has designed the 120X with an eye toward sustainability. The machine’s operation is remarkably clean, using water and garnet as the primary cutting media, which are both environmentally benign. This not only ensures compliance with stringent environmental regulations but also improves the work environment for operators by eliminating the risks associated with toxic cutting methods.
Furthermore, the energy efficiency of the Generation 4 EnduroMAX pump reduces electrical consumption, which is an increasingly crucial factor for businesses looking to decrease their operational costs and environmental impact.
OMAX 120X Abrasive Water Jet Pros and Cons
Pros
- High Precision and Speed: Equipped with IntelliTRAX linear drive technology, it offers industry-leading precision (±0.001″ linear positional accuracy) and the fastest cutting speeds.
- Advanced Software Integration: The IntelliMAX Premium Software enhances usability and efficiency, translating complex CAD designs into precise cutting instructions seamlessly.
- Versatility in Materials: Capable of cutting a wide array of materials from metals to glass and plastics without inducing heat-affected zones or mechanical stresses.
- Environmental and Operational Efficiency: Operates cleanly using water and garnet, avoiding noxious gases and minimizing electrical consumption with high-efficiency pumps.
- Reduced Setup Time: No tool changes and minimal fixturing required, which significantly cuts down setup times and boosts throughput.
- Enhanced Productivity Features: Includes a programmable Motorized Z-Axis and an optional DualBRIDGE system to double machining capacity.
- Quiet Operation: Maintains a low noise level (below 80 dBA) with Rapid Water Level Control for submerged cutting, enhancing workplace environment.
- Robust Design and Low Maintenance: Features like scissor-style hard plumbing and sealed drive systems contribute to durability and lower maintenance needs.
- Comprehensive Customer Support: Offers unlimited free training, software upgrades, and a 2-year / 4000-hour limited warranty with extensive onsite training post-installation.
Cons
- Space Requirements: Requires a considerable amount of space due to its large footprint, which may not be suitable for smaller facilities.
- Initial Cost: The high upfront investment might be a barrier for small to medium enterprises.
Customer Support and Warranty
OMAX’s customer support extends beyond the sale with a comprehensive service and training program. The lifetime free training and software upgrades ensure that users remain at the cutting edge of technology, maximizing their investment. The three-day onsite training program post-installation helps in smoothing the transition and ramp-up periods, which are critical for achieving quick ROI.
Conclusion
The OMAX 120X Precision JetMachining Center is a standout performer in the realm of large-scale and precision manufacturing. With its advanced features, robust design, and dedicated support, it offers an unparalleled solution for industries requiring precise, efficient, and reliable cutting capabilities.
For businesses aiming to boost productivity while ensuring quality, the OMAX 120X is an investment that promises substantial returns.