The OMAX 5555 Precision JetMachining Center stands out as a compact yet robust solution for medium-scale machining needs. This machine is designed to fit the needs of shops looking to maximize efficiency in a smaller footprint while maintaining the ability to handle a wide variety of materials.
In this review, we delve deep into its features, performance, and overall value to help potential users gauge whether it’s the right investment for their machining requirements.
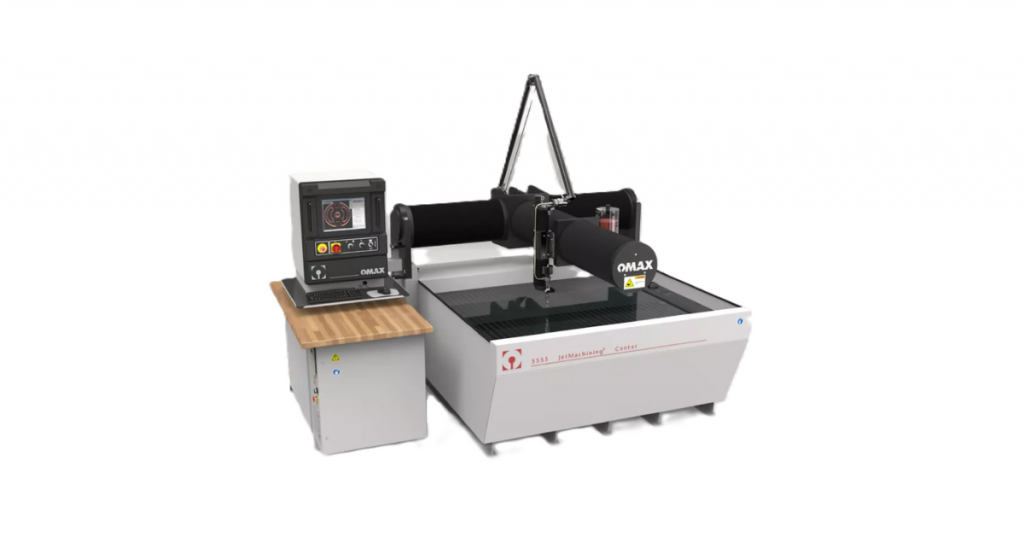
OMAX 5555 Abrasive Water Jet Specifications
Specification | Details |
---|---|
Footprint (with Pump) | 11′ 5″ x 8′ 9″ (3.48 m x 2.67 m) |
Height (with Scissor Plumbing) | 10′ (3.05 m) |
Operating Weight | 14,142 lb (6,415 kg) |
Weight (Tank Empty) | 6,220 lb (2,821 kg) |
X-Y Cutting Travel | 4′ 7″ x 4′ 7″ (1.39 m x 1.39 m) |
Z-Axis Travel (with Motorized Z-Axis) | 8″ (203 mm) |
Table Size | 6′ 8″ x 5′ 5″ (2.03 m x 1.65 m) |
Material Supports Slats | 4″ x 1/8″ Galvanized Steel |
Maximum Supported Material Load | 400 lbs/sq ft (1,950 kg/sq meter) |
Electrical Requirements | 3-Phase, 380-480 VAC ±10%, 50-60 Hz |
Noise Level | Below 80 dBA at one meter for submerged cutting |
Speed | 180 in/min (4.57 m/min) |
Linear Positional Accuracy | ±0.001″ (±0.025 mm) |
Repeatability | ±0.001″ (±0.025 mm) |
Ballbar Circularity | ±0.0025″ (±0.064 mm) |
Quick Features Look
Standard Features
- IntelliMAX Premium Software: Backed by our exclusive software, enhancing operational efficiency and ease of use.
- IntelliTRAX System: Features an exclusive abrasive jet linear drive system that delivers speeds up to 350 in/min (8.9 m/min) with real-time closed-loop positioning feedback for precision.
- Programmable Z-Axis: Offers a 12-inch (305 mm) programmable Z axis, boasting the lowest ceiling height requirement in the industry.
- Rapid Water Level Control: Standard feature that ensures cleaner, safer, and quieter submerged cutting, typically maintaining noise levels below 80 dBA.
OMAX Benefits
- Local Manufacturing: Designed and manufactured at the OMAX factory in Kent, Washington, USA, ensuring high quality and reliability.
- No Heat-Affected Zones: The cutting process does not create heat-affected zones or mechanical stresses, preserving the integrity of the materials.
- Versatile Material Handling: Capable of machining a wide range of materials and thicknesses, including metals, composites, glass, and plastics.
- Efficient Setup: Requires no tool changes and minimal fixturing, which significantly reduces setup time.
Service & Training
- Lifetime Training: Unlimited free training for the life of your machine, ensuring your team is always up to speed with the latest operational techniques.
- Software Upgrades: Unlimited software upgrades are provided for the life of the machine, keeping it current with the latest improvements.
- Warranty: Comes with a 2-year / 4000-hour limited warranty, offering peace of mind and protection for your investment.
- Onsite Training: Includes 3 days of onsite training upon installation to ensure your team is fully equipped to use the machine effectively from day one.
Compact Design and Technical Specifications
The OMAX 5555 boasts a modest footprint of 11′ 5″ x 8′ 9″ (3.48 m x 2.67 m), making it an ideal choice for workshops where space is at a premium. Despite its compact size, it does not compromise on the range of capabilities. The machine’s height, with scissor plumbing, extends to 10′ (3.05 m), and it carries a substantial operating weight of 14,142 lb (6,415 kg), which underscores its sturdy build and stability.
Key specifications include an X-Y cutting travel of 4′ 7″ x 4′ 7″ (1.39 m x 1.39 m), and a Z-axis travel of 8″ (203 mm) with a motorized Z-axis that enhances precision and productivity. The table size is generous at 6′ 8″ x 5′ 5″ (2.03 m x 1.65 m), and the machine can support a maximum material load of 400 lbs/sq ft (1,950 kg/sq meter). Such dimensions and capabilities make the OMAX 5555 exceptionally versatile for a range of industrial applications.
Cutting Performance and Features
At the heart of the OMAX 5555’s performance is its IntelliMAX Premium Software, which drives the fastest cutting speeds and best precision achievable by any machine in its class. The software optimizes the cutting paths based on real-world data, which substantially reduces waste and increases efficiency.
The programmable Motorized Z-Axis and the precision OMAX MAXJET 5i Nozzle Assembly are pivotal in boosting productivity. They ensure accurate cuts, reducing the need for secondary finishing processes. Furthermore, the Rapid Water Level Control feature allows for cleaner, quieter, and safer submerged cutting, maintaining noise levels below 80 dBA—ideal for maintaining a more comfortable working environment.
The inclusion of a 600 lb Bulk Abrasive Delivery System is another noteworthy feature, which seamlessly transports garnet from a large hopper to the Zero Downtime Hopper on the Z-axis, ensuring continuous operation without pauses for refilling the abrasive.
Material Versatility and Safety Features
The OMAX 5555 can machine a vast array of materials—from metals and composites to glass and plastics—without creating heat-affected zones or mechanical stresses. This capability is particularly valuable for industries where material integrity is critical.
Safety is also a prominent aspect of the OMAX 5555. Standard scissor-style hard plumbing confines high-pressure components, enhancing safety and reliability while contributing to the machine’s reduced maintenance needs.
Service, Support, and Training
OMAX’s commitment to customer support is evident in their offer of unlimited free training for the life of the machine, unlimited software upgrades, and a 2-year / 4000-hour limited warranty. Moreover, the machine comes with three days of onsite training upon installation, ensuring that operators can maximize the machine’s capabilities from the get-go.
Advanced Pump Technology: The EnduroMAX Advantage
One of the defining features of the OMAX 5555 is its integration with the EnduroMAX pump, a high-efficiency Generation 4 system available in 30, 40, or 50 hp configurations. These pumps are not only designed to maximize performance but also to increase the longevity and reduce the operational costs of the system. The EnduroMAX pump is engineered to offer maintenance cycles after every 1,000 hours of use, which is notably longer than many competing systems. This extended maintenance interval ensures consistent performance and reduces downtime, providing a significant advantage for businesses focusing on productivity and cost-efficiency.
Ease of Use and Operational Efficiency
The OMAX 5555 is designed with the operator in mind. Easy access to the work area and minimal fixturing requirements dramatically reduce setup times and streamline the production process. The absence of tool changes further enhances the machine’s operational efficiency, allowing operators to switch between different types of materials quickly without extensive downtime for retooling.
Furthermore, the machine’s programming capabilities are user-friendly yet powerful. Operators can benefit from the intuitive layout of the IntelliMAX software, which simplifies complex cutting operations and optimizes machine paths for accuracy and speed. The ability to handle complex cuts with such ease is a testament to the sophisticated engineering behind the OMAX 5555.
Environmental Considerations and Noise Control
Environmental impact is an increasingly important consideration for modern manufacturing practices. The OMAX 5555 addresses this with its Rapid Water Level Control for submerged cutting, which not only reduces noise pollution but also minimizes the generation of airborne particles, making it a safer choice for operators and more environmentally friendly.
The noise level for submerged cutting remains below 80 dBA at one meter, which is significantly lower than many industrial machines. This feature is particularly important in shared workspaces or facilities located in noise-sensitive areas, allowing the OMAX 5555 to operate without disturbing the surrounding environment.
OMAX 5555 Abrasive Water Jet Pros and Cons
Pros
- Compact Footprint: Ideal for shops with limited space, allowing for efficient use of workshop areas without sacrificing capability.
- High Precision and Efficiency: Equipped with IntelliMAX Premium Software and a Motorized Z-Axis, it offers superior cutting precision and speed.
- Versatile Material Handling: Capable of cutting a wide range of materials including metals, composites, glass, and plastics without inducing mechanical stresses or heat-affected zones.
- Advanced Pump Technology: Features the high-efficiency Generation 4 EnduroMAX pump which requires maintenance only every 1,000 hours, enhancing operational uptime.
- Environmental and Safety Benefits: Includes features like Rapid Water Level Control for quieter, cleaner operations and scissor-style hard plumbing for increased safety.
- Comprehensive Training and Support: OMAX provides unlimited free training, software upgrades for the life of the machine, and extensive customer support.
- User-Friendly: Offers easy operator access to the work area and minimal fixturing requirements, reducing setup times and simplifying operations.
- Noise Control: Operates below 80 dBA for submerged cutting, making it suitable for noise-sensitive environments.
Cons
- Initial Cost: The upfront investment might be considerable, which could be a barrier for smaller operations or those with limited budgets.
- Space Requirements: Despite its compact design, the required space for safe and efficient operation, including areas for material handling and maintenance, might still be substantial.
- Dependency on Power Supply: Requires a 3-phase, 380-480 VAC power supply, which might not be readily available in all settings or might require additional setup.
Long-Term Value and Return on Investment
While the upfront cost of the OMAX 5555 may be considerable, the long-term value it offers through its durable construction, low maintenance requirements, and high-efficiency operation can result in a substantial return on investment. The machine’s ability to handle diverse materials and its advanced features reduce the need for multiple machines, further saving space and resources for businesses.
The comprehensive warranty and the support services provided by OMAX underscore their confidence in the product and their commitment to customer satisfaction. These elements, combined with the machine’s robust performance, make it a worthwhile investment for businesses looking to enhance their precision machining capabilities.
Conclusion
The OMAX 5555 Precision JetMachining Center stands out in the market for its advanced technology, compact design, and exceptional versatility. Its ability to efficiently cut a wide range of materials, user-friendly software, and environmentally conscious features make it an ideal choice for any shop needing precise and reliable medium-scale machining. Coupled with OMAX’s excellent training and support services, the 5555 model is not just a machine but a comprehensive machining solution that promises to drive productivity and innovation in any workshop setting.
The OMAX 5555 offers a combination of precision, efficiency, and ease of use, making it a superior choice for businesses aiming to stay competitive in a fast-evolving industry. Whether for specialized projects or routine production, this machine delivers consistent quality and performance, ensuring that it remains a valuable asset for any machining center.