In the realm of precision cutting, the need for equipment that combines efficiency, precision, and compact design is ever-growing. The OMAX 2626 Precision JetMachining Center emerges as a solution, especially for space-constrained workshops.
This review dives into its features, performance, and overall value, providing a comprehensive analysis of what makes it stand out in the abrasive water jet market.
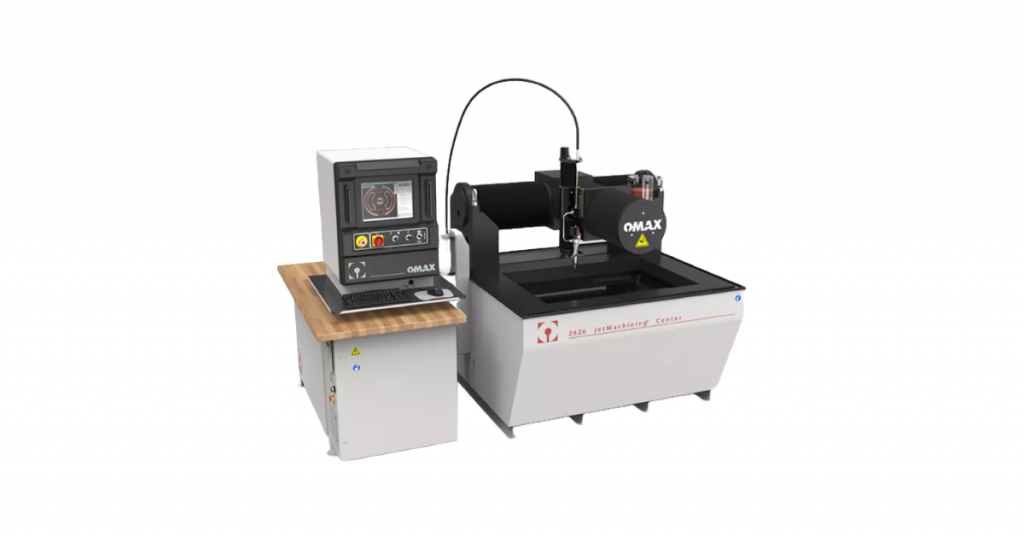
OMAX 2626 Abrasive Water Jet Review Specifications
Specification | Details |
---|---|
Footprint (with Pump) | 9′ 9″ x 6′ 10″ (2.97 m x 2.08 m) |
Height (with Whip Plumbing) | 8′ (2.44 m) |
Operating Weight | 7,393 lb (3,353 kg) |
Weight (Tank Empty) | 3,800 lb (1,742 kg) |
X-Y Cutting Travel | 2′ 2″ x 2′ 2″ (0.66m x 0.66 m) |
Z-Axis Travel (Motorized) | 8″ (203 mm) |
Table Size | 3′ 10″ x 2′ 7″ (1.17 m x 0.79 m) |
Material Supports Slats | 4″ x 1/8″ Galvanized Steel |
Maximum Supported Material Load | 400 lbs/sq ft (1,950 kg/sq meter) |
Electrical Requirements | 3-Phase, 380-480 VAC ±10%, 50-60 Hz |
Noise Level | Below 80 dBA at one meter for submerged cutting |
Speed | 180 in/min (4.57 m/min) |
Linear Positional Accuracy | ±0.001″ (±0.025 mm) |
Repeatability | ±0.001″ (±0.025 mm) |
Ballbar Circularity | ±0.0025″ (±0.064 mm) |
Quick Features Look
Standard Features
- IntelliMAX Premium Software: Backed by our exclusive software, enhancing operational efficiency and ease of use.
- IntelliTRAX System: Features an exclusive abrasive jet linear drive system that delivers speeds up to 350 in/min (8.9 m/min) with real-time closed-loop positioning feedback for precision.
- Programmable Z-Axis: Offers a 12-inch (305 mm) programmable Z axis, boasting the lowest ceiling height requirement in the industry.
- Rapid Water Level Control: Standard feature that ensures cleaner, safer, and quieter submerged cutting, typically maintaining noise levels below 80 dBA.
OMAX Benefits
- Local Manufacturing: Designed and manufactured at the OMAX factory in Kent, Washington, USA, ensuring high quality and reliability.
- No Heat-Affected Zones: The cutting process does not create heat-affected zones or mechanical stresses, preserving the integrity of the materials.
- Versatile Material Handling: Capable of machining a wide range of materials and thicknesses, including metals, composites, glass, and plastics.
- Efficient Setup: Requires no tool changes and minimal fixturing, which significantly reduces setup time.
Service & Training
- Lifetime Training: Unlimited free training for the life of your machine, ensuring your team is always up to speed with the latest operational techniques.
- Software Upgrades: Unlimited software upgrades are provided for the life of the machine, keeping it current with the latest improvements.
- Warranty: Comes with a 2-year / 4000-hour limited warranty, offering peace of mind and protection for your investment.
- Onsite Training: Includes 3 days of onsite training upon installation to ensure your team is fully equipped to use the machine effectively from day one.
Compact and Capable
The OMAX 2626 is distinctly designed for small to medium-sized shops. Despite its compact footprint, measuring just 9′ 9″ x 6′ 10″, it does not sacrifice performance. The machine offers a cutting envelope of 2′ 2″ x 2′ 2″, which is optimal for most moderate-sized projects. With its minimal floorspace utilization, the 2626 is particularly appealing for environments where every inch of space counts but operational capability cannot be compromised.
Precision Cutting with Advanced Technology
At the heart of the 2626’s efficiency is the IntelliMAX Premium Software, which is engineered to maximize cutting speeds and enhance precision. This software facilitates the use of real-world cutting data to optimize performance continually. Moreover, the system is supported by a programmable Motorized Z-Axis with a precision OMAX MAXJET 5i Nozzle, which significantly boosts productivity. The ±0.001″ linear position accuracy and repeatability ensure that each piece is cut with the utmost precision, making it suitable for intricate designs and demanding specifications.
Versatility in Materials
One of the significant advantages of the OMAX 2626 is its versatility. The machine can process a wide array of materials ranging from metals and composites to glass and plastics. This ability is particularly valuable in shops that work with diverse material types, as it eliminates the need for multiple machines and extensive tool changes. Additionally, the cutting process is clean, as it doesn’t create heat-affected zones or mechanical stresses, preserving the integrity of the materials being cut.
Environmental and Operational Efficiency
The OMAX 2626 is designed with environmental concerns in mind. It operates without producing noxious gases, liquids, or oils, aligning with modern standards for environmentally friendly manufacturing practices. Its operation is both quiet and clean, typically staying below 80 dBA at one meter during submerged cutting, which is crucial for maintaining a comfortable workplace environment. Furthermore, the efficiency of the Gen 4 EnduroMAX pump system allows for a significant reduction in maintenance requirements, with cycles occurring every 1,000 hours, enhancing operational uptime.
Training and Support
OMAX emphasizes customer support and training with the 2626. Unlimited free training for the life of the machine and unlimited software upgrades ensure that operators can continually refine their skills and utilize the latest advancements in machining technology. The initial offering includes three days of onsite training upon installation, which helps integrate the system smoothly into existing operations.
Optional Features and Customization
For shops needing even greater precision, the optional Tilt-A-Jet cutter head can be added. This feature compensates for the taper in abrasive jet cutting, ensuring that the finished edges are perfectly perpendicular. It’s an example of how the OMAX 2626 can be tailored to meet more specialized cutting needs.
Enhanced Safety and Operational Comfort
Safety and operational comfort are paramount in workshop environments, and the OMAX 2626 addresses these concerns adeptly. The standard Rapid Water Level Control feature allows for submerged cutting, which not only minimizes noise but also significantly reduces splash and mist, creating a safer and cleaner working environment. This feature, coupled with the machine’s ability to operate quietly, ensures that workplace safety and comfort standards are not just met but exceeded, making long operational hours less strenuous for operators.
Low Maintenance and High Reliability
Reliability is a critical factor for any machinery investment, and the OMAX 2626 shines in this area. The system’s low-maintenance requirements are largely due to its scissor-style hard plumbing and a drive system that’s sealed against water, dirt, and grit, which are common in harsh workshop conditions. These design choices result in fewer mechanical failures and lower maintenance costs over time. Moreover, the robust build quality and materials used in the 2626 ensure that it can withstand the rigors of continuous industrial use without compromising on performance.
Economic Efficiency
While the upfront cost of a precision cutting system like the OMAX 2626 can be significant, the machine’s economic efficiency is evident in its low operational costs. The machine’s high efficiency and speed translate into shorter production times, thus reducing labor costs and increasing throughput. Additionally, the precise cutting reduces material waste, and the lack of tool changes and minimal fixturing required further reduce operational costs. For businesses focusing on cost-efficiency without sacrificing quality, the OMAX 2626 provides a compelling return on investment.
User-Friendly Interface
Ease of use is another critical feature of the OMAX 2626. The IntelliMAX software is not only powerful but also user-friendly, designed to be accessible to operators of varying skill levels. The interface simplifies the setup for cuts, even allowing less experienced operators to achieve optimal results with minimal training. This accessibility is crucial for shops looking to quickly onboard new staff or for those that rotate through multiple operators.
Performance and Real-World Applications
The practical applications of the OMAX 2626 are extensive. Its ability to handle a diverse range of materials makes it an ideal choice for industries such as aerospace, automotive, and electronics, where precision and material integrity are crucial. Additionally, the fine quality of the satin-smooth edges produced by the 2626 reduces or even eliminates the need for secondary finishing processes, which can be particularly beneficial in custom manufacturing and prototyping scenarios.
OMAX 2626 Abrasive Water Jet Review Pros and Cons
Pros
- Compact Design: Ideal for space-constrained shops, offering a small footprint without compromising on capabilities.
- High Precision and Accuracy: Features ±0.001″ linear position accuracy, ensuring exact cuts and consistent performance.
- Versatile Material Handling: Capable of cutting a wide range of materials, from metals to plastics, without creating heat-affected zones or mechanical stresses.
- IntelliMAX Premium Software: Enhances cutting speeds and precision with an easy-to-use interface that optimizes performance.
- Environmental and Operational Efficiency: Operates quietly and cleanly, with a focus on environmental friendliness due to non-use of noxious gases and minimal electrical consumption.
- Low Maintenance and High Reliability: Designed with scissor-style hard plumbing and a sealed drive system to reduce maintenance needs and increase reliability.
- Enhanced Safety Features: Includes Rapid Water Level Control for safer, quieter submerged cutting, promoting a better work environment.
- Robust Support and Training: Offers unlimited free training and software upgrades for the life of the machine, plus extensive customer support.
- Economic Efficiency: Reduces operational costs through efficient cutting speeds, minimal material waste, and reduced labor costs due to automation.
Cons
- Initial Cost: The upfront investment might be high, which could be a barrier for smaller operations or startups.
- Space Requirements: Despite its compact size, the required space for safe and efficient operation, including access for maintenance, might still be significant for very small shops.
Customer and Community Support
OMAX’s commitment to its customers extends beyond the sale with a promise of continuous support. This includes a two-year or 4000-hour limited warranty, which underscores the company’s confidence in its products’ durability and reliability. The active user community and customer service provide a network of support for troubleshooting, tips, and sharing best practices, enhancing the overall user experience and fostering a sense of community among users.
Conclusion
The OMAX 2626 Precision JetMachining Center stands out for its compact size, high precision, and versatility. Its design and features cater effectively to space-challenged environments without compromising on performance. The robust support and training options provided by OMAX ensure that users can maximize the potential of this machine over its lifecycle.
With its capabilities, the OMAX 2626 is an excellent investment for small to medium-sized shops looking to expand their precision machining capabilities.