In the realm of precision cutting, the OMAX 2652 Precision JetMachining Center stands out as a testament to advanced engineering and user-centric design. This compact yet powerful machine provides an optimal solution for space-constrained workshops without compromising on the capability to handle a wide variety of materials and thicknesses.
The following review dives into the features, performance, and overall value of the OMAX 2652, providing insights into why it could be an essential addition to your manufacturing floor.
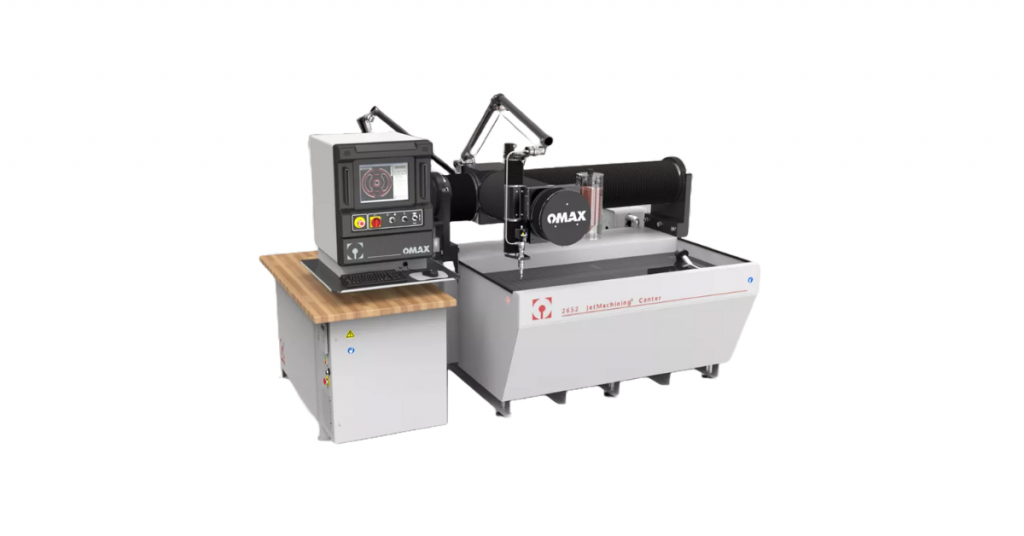
OMAX 2652 Abrasive Water Jet Specifications
Specification | Details |
---|---|
Footprint (with pump) | 12′ 1″ x 6′ 3″ (3.68 m x 1.91 m) |
Height (with scissor plumbing) | 8′ (2.44 m) |
Operating Weight | 10,252 lb (4,650 kg) |
Weight (Tank Empty) | 4,300 lb (1,950 kg) |
X-Y Cutting Travel | 4′ 4″ x 2′ 2″ (1.32 m x 0.66 m) |
Z-Axis Travel (with motorized Z-axis) | 8″ (203 mm) |
Table Size | 5′ 9″ x 2′ 6″ (1.75 m x 0.76 m) |
Material Supports Slats | 4″ x 1/8″ Galvanized Steel |
Maximum Supported Material Load | 400 lbs/sq ft (1,950 kg/sq meter) |
Electrical Requirements | 3-Phase, 380-480 VAC ±10%, 50-60 Hz |
Noise Level | Below 80 dBA at one meter for submerged cutting |
Speed | 180 in/min (4.57 m/min) |
Linear Positional Accuracy | ±0.001″ (±0.025 mm) |
Repeatability | ±0.001″ (±0.025 mm) |
Ballbar Circularity | ±0.0025″ (±0.064 mm) |
Quick Features Look
Standard Features
- IntelliMAX Premium Software: Backed by our exclusive software, enhancing operational efficiency and ease of use.
- IntelliTRAX System: Features an exclusive abrasive jet linear drive system that delivers speeds up to 350 in/min (8.9 m/min) with real-time closed-loop positioning feedback for precision.
- Programmable Z-Axis: Offers a 12-inch (305 mm) programmable Z axis, boasting the lowest ceiling height requirement in the industry.
- Rapid Water Level Control: Standard feature that ensures cleaner, safer, and quieter submerged cutting, typically maintaining noise levels below 80 dBA.
OMAX Benefits
- Local Manufacturing: Designed and manufactured at the OMAX factory in Kent, Washington, USA, ensuring high quality and reliability.
- No Heat-Affected Zones: The cutting process does not create heat-affected zones or mechanical stresses, preserving the integrity of the materials.
- Versatile Material Handling: Capable of machining a wide range of materials and thicknesses, including metals, composites, glass, and plastics.
- Efficient Setup: Requires no tool changes and minimal fixturing, which significantly reduces setup time.
Service & Training
- Lifetime Training: Unlimited free training for the life of your machine, ensuring your team is always up to speed with the latest operational techniques.
- Software Upgrades: Unlimited software upgrades are provided for the life of the machine, keeping it current with the latest improvements.
- Warranty: Comes with a 2-year / 4000-hour limited warranty, offering peace of mind and protection for your investment.
- Onsite Training: Includes 3 days of onsite training upon installation to ensure your team is fully equipped to use the machine effectively from day one.
Compact Design and Robust Construction
The OMAX 2652 features a notably compact footprint measuring 12′ 1″ x 6′ 3″ (3.68 m x 1.91 m), making it ideal for smaller shops that need to maximize their usable space. Despite its small size, it doesn’t skimp on power or capability, supporting an impressive maximum material load of 400 lbs/sq ft (1,950 kg/sq meter) on its 5′ 9″ x 2′ 6″ (1.75 m x 0.76 m) table.
The construction of the OMAX 2652 emphasizes durability and precision. With pre-loaded linear bearings and precision ball screws, it achieves a high degree of accuracy, maintaining a linear positional accuracy and repeatability of ±0.001″ (±0.025 mm). The inclusion of scissor-style hard plumbing not only enhances safety by containing high-pressure components but also contributes to the system’s overall reliability and ease of maintenance.
Cutting Performance and Software Integration
At the heart of the OMAX 2652’s performance is the IntelliMAX Premium Software, which is designed to optimize cutting paths for speed and precision. The software is intuitive and supports the machine’s ability to handle everything from metals and composites to glass and plastics, without creating heat-affected zones or mechanical stresses.
The machine’s Programmable Motorized Z-Axis and the OMAX MAXJET 5i Nozzle enhance its productivity, enabling precise control over the cutting head and effectively boosting process efficiency. The optional Tilt-A-Jet accessory further enhances precision by compensating for the taper typically associated with abrasive jet cutting, thereby delivering perpendicular cuts with minimal angular deviation.
Innovative Features for Enhanced Usability
One of the standout features of the OMAX 2652 is its Rapid Water Level Control, which allows for quieter and cleaner submerged cutting, typically maintaining noise levels below 80 dBA. This feature not only improves the working environment but also reduces the production of debris and splash-back, which can be crucial in maintaining a clean shop floor.
The EnduroMAX Pump, available in 30, 40, or 50 hp configurations, is another significant addition, providing a robust pumping solution that maximizes nozzle horsepower and efficiency. The pump is designed for easy maintenance, with scheduled cycles every 1,000 hours, emphasizing uptime and reliability.
Environmental Considerations and Material Flexibility
The OMAX 2652 is designed with environmental considerations at the forefront. It operates without the need for noxious gases, liquids, or oils, making it a more sustainable choice for machining. Its ability to cut a wide range of materials, from delicate glass to robust metals, without the need for multiple tool changes or extensive fixturing, dramatically reduces setup time and increases throughput.
Training and Support
OMAX stands behind the 2652 with a robust support system, including unlimited free training for the life of the machine and unlimited software upgrades. Additionally, the company offers three days of onsite training upon installation, ensuring that operators can maximize the machine’s capabilities and maintain it properly. The 2-year / 4000-hour limited warranty provides further peace of mind, highlighting OMAX’s commitment to quality and customer satisfaction.
Operational Efficiencies
The OMAX 2652 not only delivers on the front of cutting technology but also excels in operational efficiencies, which can significantly impact productivity and cost-effectiveness. The machine’s speed of up to 180 in/min (4.57 m/min) allows for rapid production cycles, essential for high-throughput environments. Additionally, the Variable Speed Solids Removal System (VS-SRS) is a noteworthy feature, designed for industrial use to increase uptime through automated solids removal. This system efficiently manages the by-products of the cutting process, maintaining the integrity of the cutting tank and reducing the downtime associated with manual cleanouts.
Moreover, the motorized Z-axis enhances component life and reduces the wear and tear on critical machine parts by allowing precise control over the nozzle’s distance from the material, adapting automatically to variations in material height. This precision not only extends the life of the nozzle and other consumables but also ensures consistent cutting quality across different materials and thicknesses.
Customer Service Excellence
OMAX’s commitment to supporting their products is clearly demonstrated through their comprehensive service offerings. The availability of unlimited free training and software upgrades for the life of the machine ensures that users can continually refine their operational skills and keep the software up-to-date with the latest features and improvements. This commitment extends to a robust warranty and responsive customer service, providing users with assurance and support whenever needed.
The inclusion of three days of onsite training upon installation is particularly beneficial for new users, as it helps in smoothing the initial learning curve associated with any sophisticated machinery. This training covers not only the basic operation of the machine but also advanced techniques to optimize the machine’s performance for specific applications, ensuring that users can start on a strong footing.
OMAX 2652 Abrasive Water Jet Pros and Cons
Pros
- Compact Footprint: Ideal for space-constrained workshops, allowing for optimal utilization of floor space without sacrificing performance.
- High Precision and Accuracy: Delivers ±0.001″ (±0.025 mm) linear position accuracy and repeatability, suitable for intricate and detailed cutting requirements.
- Versatility in Material Handling: Capable of cutting a wide array of materials including metals, composites, glass, and plastics without the need for tool changes, reducing setup time.
- Advanced Software Integration: Comes with IntelliMAX Premium Software, which optimizes cutting paths for the fastest speeds and best precision based on real-world cutting data.
- Environmental Friendliness: Operates without generating noxious gases, liquids, or oils, promoting a cleaner, safer work environment.
- Low Maintenance and High Reliability: Features such as scissor-style hard plumbing and a sealed drive system enhance reliability and reduce maintenance needs.
- Quiet Operation: Maintains noise levels below 80 dBA during submerged cutting, enhancing workplace comfort.
- Comprehensive Customer Support: Includes unlimited free training and software upgrades for the life of the machine, plus three days of onsite training upon installation.
- Efficient Water Management: Rapid Water Level Control for cleaner, quieter submerged cutting and a Variable Speed Solids Removal System to automate waste management.
Cons
- Initial Cost: The upfront cost might be higher compared to less sophisticated machinery, which could be a barrier for smaller operations or startups.
- Space Requirements: Despite its compact design, the need for additional space for safe operation and maintenance might still be considerable.
Long-Term Benefits
Investing in the OMAX 2652 can bring substantial long-term benefits to any workshop. The machine’s ability to handle a diverse range of materials from metals to plastics without requiring tool changes reduces both the time and cost associated with tool procurement and setup. This versatility makes the OMAX 2652 an excellent choice for shops that work with a broad portfolio of products.
The environmental benefits of using a water jet, which does not generate hazardous waste nor require cooling or lubricating oils, make it a preferable option for companies looking to reduce their environmental footprint. This factor is increasingly important in industries where environmental impact is closely monitored and can even be a deciding factor when clients choose between vendors.
Conclusion
The OMAX 2652 Precision JetMachining Center is a powerful ally in the precision cutting industry, offering remarkable flexibility, efficiency, and precision in a compact package. Its design and technological innovations not only meet the demands of a wide range of industries but do so in a way that emphasizes usability, reliability, and environmental responsibility. For workshops looking to upgrade their cutting capabilities with minimal space impact, the OMAX 2652 represents a smart, strategic investment.